Clydebridge Steelworks 1887 - present
By Colin Findlay
© Rutherglen Heritage Society
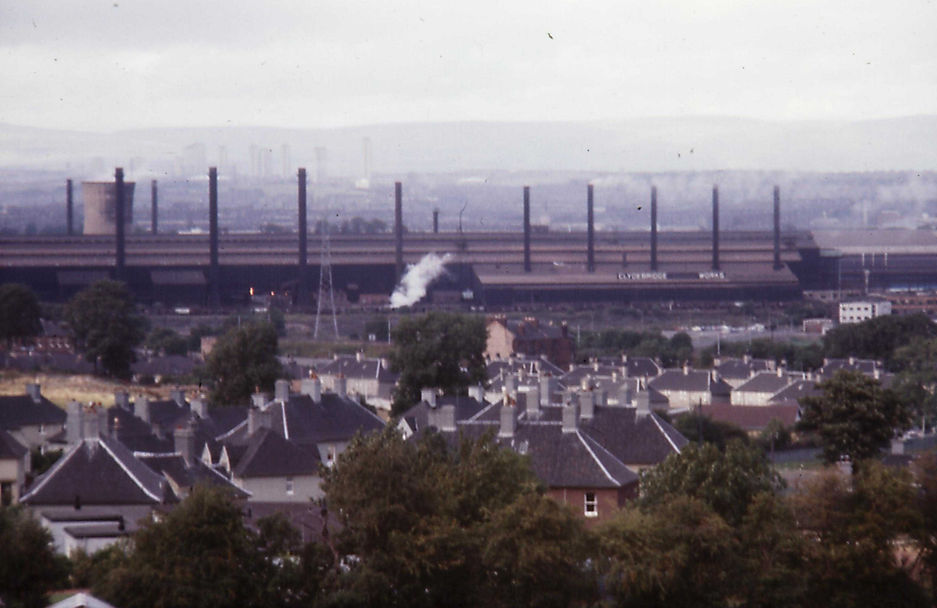
Above, Clydebridge Steelworks, September 1973
Steel has been made in Scotland since at least the 16th Century but the real market for steel was when shipbuilders started to adopt it in place of malleable iron, in the late 1870s.
​
In 1872 the Steel Company of Scotland, at Hallside, was one of the first to start production using the new Siemens Open Hearth Furnaces and had an initial monopoly, but many other companies started up, or converted from malleable iron to steel. This created a lot of competition and not all survived.
The Clydebridge Steel Company Ltd was one that only just survived, but which went on to thrive. It was started in 1887 by the Neilson family at a cost of £90,000, two thirds of which was provided by the Neilson family. Quotes for construction of the works were obtained in 1885, and by 1887 the works were largely constructed and the workforce was being hired.
​
It was started by the Nielson family, related to James Beaumont Nielson, famous for the hot blast process, first tried at Clyde Iron Works. Hugh Neilson ran the Mossend Iron Co but retired in 1886 to set up Clydebridge. The original manager of Clydebridge was James Neilson, He was anti-trade unions and offered low wages. Production started in 1888 but, by September 1889, 13 unionists had been sacked and a strike shut the works for four months.

Before the First World War there was a low demand for steel and Clydebridge was closed for 5 years, from November 1907 to November 1912, under a subsidy from the Scottish Steelmakers Association to control demand.
​
With the outbreak of war, in 1914, there was a sudden need for steel billets to make high explosive shells and in 1915 David Colville and Sons, based in Motherwell, was asked to lease and extend Clydebridge and Glengarnock steelworks.
The enlargement of both works began in October 1916, at a cost of £1½ million.
Left,sampling at Clydebridge, 1974
When Clydebridge Works was taken over, in October 1915, the Melting Shop contained six 40 ton and two 60 ton open hearth furnaces, and a foundation for another large furnace. A cogging mill supplied the plate mills, of which there were three, so arranged that only two were worked at one time, No. 2 being independently driven, while No. 1 and No. 3 (No. 3 was installed in 1907) had an engine in common.
The cogging mill was altered to roll 6 inch and 8 inch shell bars, and a Shell Shop was erected, with six batteries of hack saws to cut the billets to shell lengths. A new 60 ton furnace was built on the foundation in the Melting Shop, making the total output up to about 2,000 tons of ingots a week. Extensive alterations were also carried out in other areas, with a view to speeding up the output.

Above, teeming, 1970s. This is the process of pouring molten metal from a ladle into an ingot mould
To meet the acute demand for ship plates, a large extension to the works was begun, in October 1916, comprising five 60 ton open hearth furnaces with stockyard and producer bench, and a cogging mill plus ingot soaking pits.
The No 3 ‘Heavy’ Plate Mill, which was used for rolling wide plate, was dismantled and sent to Dalzell works to be converted into a new No 2 Cogging Mill, and a steam hydraulic guillotine was added to cut the slabs to length.
Later, a new engine was installed at the independently driven No2 ‘Light’ Plate Mill and the No1 Plate Mill put into good order.
​
The new works began producing steel at the end of 1917, and in May 1918 the new cogging mill came into operation. Thereafter both plate mills were kept fully supplied with slabs, and were able to produce about 1,500 tons weekly; 2,000 people were now employed at Clydebridge.
%20red.jpg)
Above, Clydebridge Steelworks in the snow
During 1914-1918, the three works of David Colville and Sons (DaIzell, Glengarnock and Clydebridge) manufactured:
​
Shell Bars 630,859 tons
Trench Rails 29,128 tons
Bullet and Bomb-Proof, and Nickel Chrome Steel Bar, (for Aeroplanes) 9,550 tons
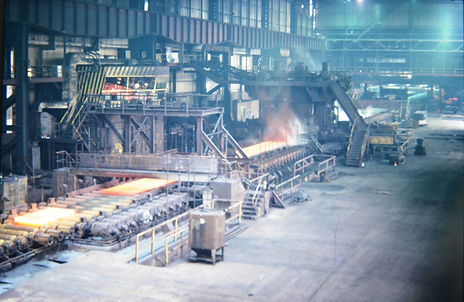
A new 3 high, electrically driven, plate mill was installed in 1922 to meet an expected demand for shipbuilding. However, a worldwide slump in trade closed the works for several months and the brand new mill was idle until the works restarted on the 20th February 1923. At this point in its history Clydebridge had survived its difficult early years and was now set to grow.
Left, Clydebridge plate mill, July 1973
By 1939, with hot metal working from Clyde Iron, Clydebridge became one of the largest integrated steelworks in the UK, setting world records for the production of sheared plates used to build most of the famous ships on the Clyde (and at Harland and Woolf in Belfast) such as the Lusitania, Mauretania, The Empress of Ireland, Queen Mary, Queen Elizabeth, QE2.
It would reach its maximum size with the addition of the 4 high plate mill and new shearing facilities in the early 1960s, and the expansion of the heat treatment plant in the 1970s.
The peak was reached in 1977, just before the widespread closure of most of the UKs open hearth melting shops and closure of the cogging mill. The plant continued to be supplied with continuously cast slabs from Ravenscraig but with the demise of shipbuilding in the UK the demand for steel plates fell and the plate mill was closed in 1982.
The heat treatment and quenching plant survived and is run as a satellite of Dalzell steelworks.
Right, cooling floor at Clydebridge, 27th. February 1975


Above, Clydebridge melting shop, December 1974
More information and photographs of Clydebridge and other Scottish steelworks can be found on Colin Findlay’s website here
Text and original photographs by Colin Findlay